信息摘要:
1引言 索具是起吊裝備與重物之間連接件的統(tǒng)稱,其具有強度高、承載能力強等優(yōu)點,因此在海洋資源開采、橋梁工程、大型工程平臺的起吊等領(lǐng)域廣泛應(yīng)用,目前已成為應(yīng)用最廣泛的
1引言
索具是起吊裝備與重物之間連接件的統(tǒng)稱,其具有強度高、承載能力強等優(yōu)點,因此在海洋資源開采、橋梁工程、大型工程平臺的起吊等領(lǐng)域廣泛應(yīng)用,目前已成為應(yīng)用最廣泛的撓性構(gòu)件之一凡壓制索具采用的標(biāo)準(zhǔn)有GB/T30589-2014《鋼絲繩繩端套管壓制素具》四、G/T16762一2009《一般用途鋼絲繩吊索特性和技術(shù)條件》風(fēng)、GB/T6946-2008《鋼絲繩鋁合金壓制接頭》、歐盟標(biāo)準(zhǔn):EN13411-3:2004《鋼絲繩端固結(jié)法第三部分:套管和套管固結(jié)》、EN13414-1:2003《鋼絲繩吊索一安全第一部分:一般提升用途吊索》等。國內(nèi)有很多學(xué)者對鋼絲繩索具進行了大量的研究,文獻通過利用ANSYS有限元軟件對lX7+IWS結(jié)構(gòu)鋼絲繩服役中的應(yīng)力應(yīng)變進行了數(shù)值模擬,文獻研究了鋼絲繩在沖擊載荷作用下的動力學(xué)特性,文獻響用ANSYS對平直鋼絲繩服役時的應(yīng)力場與疲勞壽命進行了仿真分析研究,文獻研究了適合具有內(nèi)部鋼絲繩繩芯結(jié)構(gòu)的鋼絲繩方法,建立了單獨鋼絲繩或復(fù)雜鋼絲繩結(jié)構(gòu)中繩股的軸向力、彎矩、扭矩等求解的數(shù)學(xué)模型,使鋼絲繩理論研究有了突破性的進展。華中科技大學(xué)王桂蘭教授采用共轉(zhuǎn)坐標(biāo)系彈塑性有限元法模擬了鋼絲繩捻制形成過程,用數(shù)值計算和X射線實驗探討了扭轉(zhuǎn)系數(shù)對鋼絲殘余應(yīng)力和彈性恢復(fù)變形的影響規(guī)嗎。目前索具在壓制成形方面的研究頗少,擬在研究鋼絲繩鋁合金接頭結(jié)構(gòu)設(shè)計與成形工藝的基礎(chǔ)上,運用三維實體建模與有限元相結(jié)合的方法建立索具三維實體物理結(jié)構(gòu)模型,并分析鋼絲繩索具壓制成形后索具接頭內(nèi)部的應(yīng)力分布以及所需壓制力,為索具的可靠性設(shè)計、優(yōu)化改進和壽命預(yù)測等方面的研究提供參考。
2鋼絲繩索具及其有限元模型
研究的對象是1X7+IWS-18mm單股型鋁合金壓套鋼絲繩索具,IWS代表獨立鋼芯結(jié)構(gòu),其特點是側(cè)絲沿Z軸成一次螺旋曲線形式環(huán)繞股芯捻制,同時沿x軸折返式折疊,為空間螺旋折返式自接觸鋼絲繩結(jié)構(gòu),該型號鋼絲繩自接觸類型為線接觸,但隨著壓制載荷的施加,接觸方式逐漸轉(zhuǎn)變?yōu)槊娼佑|。基于SolidWorks平臺,以單股1×7+HWS且總直徑為18mm的折返式鋼絲繩為研究對象,分別建立不同參數(shù)壓套索具三維實體模型。由于鋁套在壓制過程中會產(chǎn)生巨大的變形,因此將鋁合金套分成4部分實體進行獨立建模和裝配,以便大變形部位進行局部網(wǎng)格細(xì)化。為提高計算效率,減少網(wǎng)格數(shù)量,采用剛體殼模型代替模具整體模型,通過RemoveFaces命令完成從模具模型到剛體殼模型的轉(zhuǎn)換。
運用ABAQUS軟件對索具成形過程進行仿真分析,鋼絲繩采用C3D8R顯示實體單元進行掃略網(wǎng)格劃分,由于鋁套成形時中間會有極大的塑性變形,采用C3D8R顯示實體單元進行結(jié)構(gòu)化網(wǎng)格劃分,并細(xì)化中間區(qū)域,剛體殼模型采用C3D4單元進行自由網(wǎng)格劃分。索具壓制過程中接頭內(nèi)部的接觸狀態(tài)極為復(fù)雜,擬采用General Contact 接觸方式,由程序判斷壓制過程中的接觸狀態(tài)。利用Mises屈服準(zhǔn)則和Prandl-Reuss應(yīng)力應(yīng)變關(guān)系推導(dǎo)出彈塑性剛度矩陣,選用拉格朗日增量模擬方式進行變形模擬,運用Abaqus 自帶的Explicit 求解器進行仿真求解。相應(yīng)的索具壓制實體模型及其有限元模型,如圖1、圖2所示。
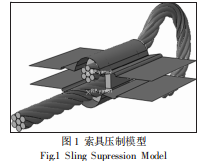
3鋼絲繩索具壓制成形應(yīng)力分析
接頭擠壓成形的原理是利用冷擠壓無切削塑性加工工藝,在不破壞金屬內(nèi)部組織結(jié)構(gòu)的前提下,使金屬體積產(chǎn)生塑性位移,從而使金屬達到成形的目的。由于冷擠壓工藝處于三向應(yīng)力狀態(tài),因而提高了金屬的塑性和變形度。操作時將鋼絲繩穿入鋁合金套,采用冷擠壓使鋁合金套和鋼絲繩在擠壓模腔內(nèi)產(chǎn)生塑性變形壓制而成。由于鋼絲繩末端插入鋁合金橢圓管內(nèi),在外力作用下,利用鋁材塑性變形特性,在套管和鋼絲繩組成的截面上,鋁合金被充分?jǐn)D入鋼絲繩股與股、絲與絲之間的間隙內(nèi),并在套管內(nèi)壁形成了與鋼絲繩表面一樣的螺旋體,即形成“多頭螺紋”的固結(jié)體。
工程實際中一種直徑的鋼絲繩對應(yīng)一種規(guī)格的鋁合金套,由于鋁套長度的修改伴隨著模具的修改,因此壁厚的大小與索具承載力密切相關(guān),壁厚的大小最直觀的結(jié)果就是延伸率,因此行業(yè)中采用控制延伸率為(25-35)%的方法實現(xiàn)索具滿足承載力的要求且成形后接頭不開裂,因此,索具成型后鋁套的延伸率成為研究的首要目標(biāo)。延伸率是描述材料塑性性能的指標(biāo),即試樣拉伸斷裂后標(biāo)距段的總變形AlL(mm)與原標(biāo)距長度L(mm)之比的百分?jǐn)?shù):
6=ALULx100%
擬采用控制變量法分析不同參數(shù)壓套索具成形過程中鋁套的延伸率和應(yīng)力分布以及鋼絲繩上的應(yīng)力分布情況,上下模具為對稱結(jié)構(gòu),模具材料選擇CrWMn,由于壓制成形后模具相對于鋁套及鋼絲繩的變形極小,且模具剛度相比繩和套的剛度高很多,因此假設(shè)模具不變形,鋼絲繩和鋁套的相關(guān)參數(shù),如表1所示。通過對(6-8③mm壁厚鋁接頭索具的分析發(fā)現(xiàn),隨著壁厚的增加,其延伸率呈現(xiàn)單調(diào)遞增的趨勢,由20.52%增長到41.97%,對應(yīng)鋼絲繩上的應(yīng)力由900MPa增加到921MPa,其中壁厚為7mm的鋁壓套其延伸率為25.53%,相應(yīng)鋼絲繩上的應(yīng)力為912MPa,鋁套延伸率符合行業(yè)指定標(biāo)準(zhǔn),接頭索具各仿真結(jié)果,如圖3-圖5所示。
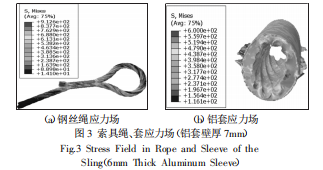
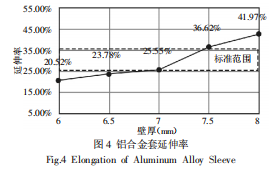
總結(jié)以上的分析,對(6~8③mm壁厚鋁壓套索具進行模具應(yīng)力分析,并著重分析7mm壁厚鋁套索具成形所需壓制力與參考壓制力大小差異。經(jīng)分析后得出,應(yīng)力值隨著壁厚的增加呈同步
增長的趨勢,其中壁厚為7mm的鋁接頭索具成形壓制力為
1097.5lkN,為最大參考壓力的68.6%,符合工程實際要求。
4鋼絲繩索具疲勞壽命分析
隨著鋼絲繩索具的長期使用,疲勞損傷或破斷現(xiàn)象時有發(fā)
生,因此,較為準(zhǔn)確地預(yù)測鋼絲繩索具疲勞壽命對預(yù)防安全事故
極為重要,為此,結(jié)合有限元軟件ABAQUS-ANSYS,將ABAQUS計算結(jié)果文件導(dǎo)入ANSYS中,并基于名義應(yīng)力法對鋼絲繩索具
的疲勞壽命進行分析。固定索具一端,對另一端施加50MPa的拉力,建立預(yù)設(shè)循環(huán)壽命為1e6次的索具虛擬疲勞壽命仿真模型,采用goodman應(yīng)力修正,設(shè)置載荷比例因子為1,對1X7+IWS-
18mm型鋼絲繩索具進行疲勞壽命分析。
ANS5|
圖6索具疲勞壽命云圖圖7鋼絲繩索具
Fig.6 Ringgng Fatigue Life Nephogram Fig.7 Wire Rope Rigging經(jīng)計算1×7+IWS-18mm型鋼絲繩索具疲勞壽命云圖,如圖6所示。對應(yīng)鋁套壁厚為7mm的鋼絲繩索具在應(yīng)力最大的位置
發(fā)生破壞,與實際斷裂位置一致,如圖7所示。該索具在承受上述
載荷時疲勞壽命為352次。改變鋁套壁厚為6mm、6.5mm、7.5mm、
8mm,索具疲勞壽命結(jié)果的變化規(guī)律,如圖8所示。由圖可知鋁套壁厚過厚或者過薄都會降低鋼絲繩的疲勞壽命:鋼絲繩疲勞壽命和應(yīng)力分布有著直接的關(guān)系,應(yīng)力越大的地方疲勞壽命越小,因
此選取合適的壁厚能提高鋼絲繩索具的疲勞壽命。
5實驗
針對以上的分析結(jié)果,采用100T鋼絲繩壓套機對1X7+IWS+
18mm型號的鋼絲繩索具進行成形壓制試驗,如下圖所示,上模與機身連接固定不動,下模具與液壓系統(tǒng)連接,通過液壓缸的推動使下模具往上運動,當(dāng)下模具運動至與上模具貼合時,索具壓制完成。
相應(yīng)的設(shè)備名稱和索具壓制結(jié)果,如圖9-圖10所示。
優(yōu)選出壁厚為7mm的鋁壓套索具進行試驗,得到鋁合金套延伸率為30%,本試驗所選模型的仿真結(jié)果壓制力為10975lkN,為最大參考壓制力的686%,延伸率為25.53%,與實際結(jié)果偏差14.9%,鋁套變形仿真結(jié)果與實際結(jié)果較吻合。
6結(jié)論
(D利用絲與絲裝配的方法建立鋼絲繩模型:將鋁合金套分成4個獨立部件進行單獨建模與裝配,有利于局部大變形部位進行網(wǎng)格細(xì)化:建立剛體殼平面來代替模具整體模型,以減少網(wǎng)格數(shù)量。
②不同壁厚鋁接頭索具的仿真結(jié)果表明,隨著鋁套壁厚的增加,成形后鋁套的延伸率呈同步增長的趨勢,由(20.52-41.97%,其中,壁厚為7mm的鋁套延伸率為25.53%,與實際結(jié)果偏差149%,滿足工程實際與行業(yè)標(biāo)準(zhǔn),為鋁套壁厚的選取提供有力的理論依據(jù)。
(3)索具成形后的應(yīng)力結(jié)果表明,7mm壁厚的鋁接頭索具成形后最大應(yīng)力為9l2MPa分布在鋼絲繩彼此接觸部位上,鋁合金套上的最大應(yīng)力為600MPa。
(41X7HWS型規(guī)格的鋼絲繩索具成形壓制力為10975lkN,為實際最大壓制力的68.6%,索具鋁接頭變形結(jié)果與實際一致,為鋼絲繩索具壓制成形提供參考價值。
()鋁套壁厚為7mm的鋼絲繩索具疲勞壽命為352次,隨著壁厚的增加或減少,對應(yīng)索具的疲勞次數(shù)呈現(xiàn)遞減的趨勢,因此,合理的選取鋁套的壁厚能提高鋼絲繩索具的疲勞壽命。